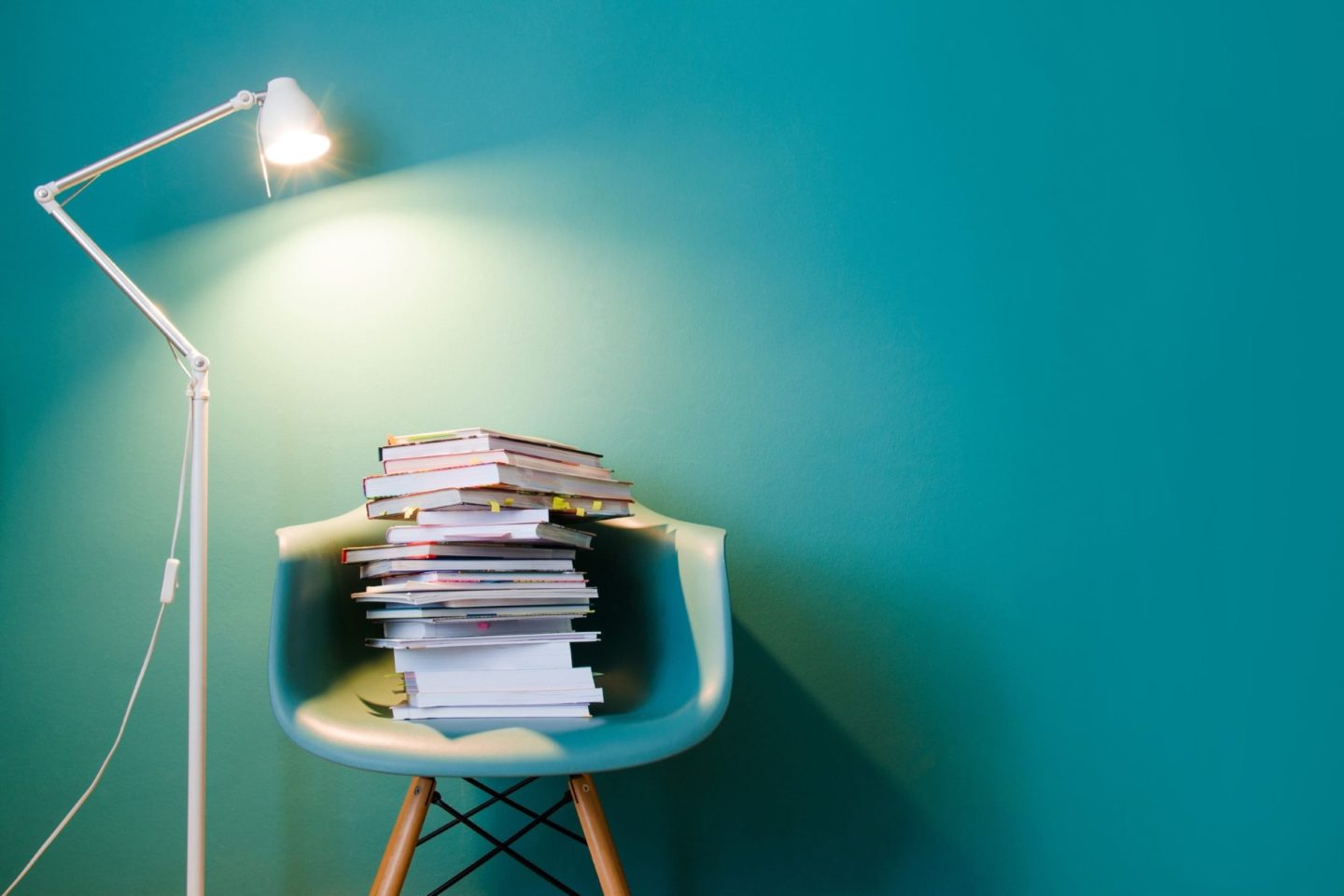
Knowledge Base
Browse our knowledge base and find out everything you need to know about circular economy and bioplastics.
Knowledgebase
Search Knowledge Base
Bioplastics
What are bioplastics?
We clarify the question of what bioplastics are, what makes them so special and where they can be used.
Find out moreRecyclates & recycled plastics
What are recyclates?
How do you define recyclates? Which plastic can be recycled? And are there differences in quality? We explain these questions and the difference between post-consumer recyclate (PCR) vs. post-industrial recyclate (PIR) in our knowledge article. If you want to know what to look out for when using a recyclate in your plastic products, then you’ve come to the right place.
Find out moreProcessing Methods
3D Printing
3D printing is an additive manufacturing process that allows components to be made without molds by printing with molten plastic materials.
Find out moreBlown film extrusion
Blown film extrusion is the most common process for the production of continuous films that are used primarily for packaging.
Find out moreExtrusion coating
In extrusion coating, plastic, paper or aluminum carrier films are combined with a thermoplastic layer to form a composite material which is bonded together.
Find out moreExtrusion blow moulding
Extrusion blow moulding (EBM) is commonly used to produce hollow parts such as bottles, canisters or irregularly shaped containers.
Find out moreLamination
Lamination is a finishing process in which a plastic film from a roll is bonded to a substrate such as paper, cardboard or aluminum foil.
Find out moreNet Extrusion
For the production of netting from thermoplastics, the material is first melted in the extruder and subsequently extruded through counter-rotating nozzles which have holes on the circumference.
Find out moreSheet extrusion
In the simplest form of sheet extrusion, plastic granules (possibly including additives) are fed from the extruder hopper along a heated cylinder by a rotating screw, melted & homogenized and conveyed to the sheet die.
Find out moreProfile extrusion
In the simplest form of profile extrusion, plastic granules (possibly including additives) are fed from the extruder hopper along a heated cylinder by a rotating screw, melted & homogenized and conveyed to the die. Depending on the application, there are a number of variations including the number and rotation of the screws, the screw and cylinder geometry and the structure. The die itself can be fed by several extruders extruding different thermoplastics, (for example recycled materials) resulting in layered or concentric co-extrudates. The die geometry that can be extremely complex and can contain undercuts. The extrudate is fed into a calibration sleeve which ensures that the profile geometry is exactly maintained. Subsequent parts of the machine convey, cool, cut and can decorate the profile.
Find out moreFoaming
Foamed thermoplastics contain bubbles that have either remained intact during processing (closed-cell) or have bonded together (open-cell foam).
Find out moreInjection blow moulding
Injection blow moulding is a multi-stage process that produces predominantly rotationally symmetric, seamless hollow bodies (for example beverage bottles) in large numbers, without waste and with a high surface quality.
Find out moreInjection moulding
Injection moulding is a process for the sequential production of one or more three-dimensional thermoplastic parts.
Find out moreThermoforming
Thermoforming, also referred to as vacuum forming or deep drawing, is a highly economical process for manufacturing products such as trays, blister packs and cup lids in large quantities.
Find out moreResearch Projects
research projects
An overview of current FKuR research projects
Find out moreSustainability
Circular economy – the 8R principles: Examples, advantages and benefits
A central approach to the circular economy is the classic 3Rs “Reduce, Reuse, Recycle”. With our “8Rs”, we have expanded this model to include additional dimensions. This more comprehensive approach reflects a maximally sustainable and resource-efficient economy. The focus is on three principles in particular….
Find out more10 Ways to live more Sustainability
We are convinced that together we can create a sustainable future! That’s why we’ve put together some simple suggestions on how we can all live our lives more consciously and make our everyday lives more sustainable.
Find out moreDefinition of sustainability
Sustainability is most often described by the following definition
Find out moreEight simple ideas for your sustainable product
Plastics and sustainability – that sounds like a contradiction in terms at first, as the mountains of waste immediately appear in our mind’s eye. How can we ensure that the elements of a responsible and sustainable circular economy are implemented in product design? We have eight simple ideas for designing recyclable products.
Find out moreNo results for this search
Frequently asked questions
Search FAQ
Bioplastics
What is the production capacity of I`m Green™ biobased polyethylene plant? Where is the plant located?
The Renewable Ethylene plant is located at the Triunfo Petrochemical Complex, in the state of Rio Grande do Sul, in the southern region of Brazil. It was inaugurated in September 2010, and it was the first time that I’m green™ bio-based polyethylene was manufactured on an industrial scale. The plant’s capacity is 260,000 tonnes/year, and its total investment is US$290 million. © Braskem 2023
Wie hoch ist die Produktionskapazität der I`m Green™-Anlage für biobasiertes Polyethylen? Wo befindet sich die Anlage?
Die Anlage für erneuerbares Ethylen befindet sich im Petrochemiekomplex Triunfo im Bundesstaat Rio Grande do Sul, im Süden Brasiliens. Sie wurde im September 2010 eingeweiht, und es war das erste Mal, dass I’m green™ biobasiertes Polyethylen in industriellem Maßstab hergestellt wurde. Die Kapazität der Anlage beträgt 260.000 Tonnen/Jahr, die Gesamtinvestition beläuft sich auf 290 Millionen US-Dollar. © Braskem 2023
What is I`m Green™ bio based logo?
I’m green™ bio-based is the brand created by Braskem that identifies the products in its portfolio made from renewable sources. To identify products that have I’m green™ bio-based polyethylene in their composition and to help consumers recognise them, Braskem created the I’m green™ bio-based label. © Braskem 2023
What is the difference between biodegradable and compostable?
Biodegradation is a chemical process in which a material is converted into CO2, water and biomass with the help of microorganisms. The process of biodegradation depends on the conditions (e.g. location, temperature, humidity, presence of microorganisms, etc.) of the environment (industrial composting plant, garden compost, soil, water, etc.) and the material or application itself. Thus, the fact that a plastic is biodegradable does not say anything about the necessary time and conditions in which a biodegradation process takes place. One specification of biodegradation is compostability. Biodegradable plastics and products are considered compostable only if they can be degraded in a specific time under defined conditions. These specific conditions are defined in standards, such as the European standard for industrial composting EN 13432 (for packaging) or EN 14995 (for plastics in general). Materials and products that comply with this standard can be certified and labeled accordingly.
What is Braskem`s I`m Green™ biobased renewable polyethylene?
Conventional polyethylene is produced from fossil raw materials, such as oil or natural gas, and is found in many day-to-day products: food packaging, cosmetics, drinks, carrier bags, among others. Renewable plastic, also known as I’m green™ bio-based renewable polythene, is a plastic produced from a renewable raw material –ethanol from Brazilian sugar cane. I’m green™ bio-based polyethylene has the same characteristics as petrochemical polyethylene in terms of application, performance and, most importantly, recycling.
© Braskem 2023
How long does it take for biodegradable plastics to degrade?
As with organic materials (e.g. wood, green waste or kitchen waste), biodegradation depends on many external factors, such as temperature, moisture, oxygen, pH, and the presence of microorganisms and fungi. In addition, the type of material and layer thickness of the product also play a decisive role in the duration of biodegradation. For example, a thin biowaste bag degrades much faster than a drinking cup, even if it is made of the same material.
What are bioplastics?
Bioplastics are a large family of different materials, not just a single material. Because the term bioplastic is not legally protected, it is not used consistently. The European Bioplastics association defines a plastic as a bioplastic if it is either bio-based or biodegradable, or has both properties. Because of this diversity, it is even more important to make it clear to the consumer what makes this plastic so different from conventional, petroleum-based plastics. Note: Bioplastics are bio-based, biodegradable or both at the same time.
What are biobased plastics?
All plastics produced on the basis of renewable raw materials are referred to as bio-based plastics. In contrast, conventional fossil plastics are produced from petroleum. Renewable raw materials include sugar from sugar cane and sugar beets, cellulose from cotton or wood, starch from corn or potatoes, and vegetable oils such as castor oil. Attempts are currently being made to use more residual and waste materials from agriculture, forestry and industry. A bio-based plastic can be made entirely or only partially from renewable raw materials. They can be biodegradable/compostable, but do not have to be. Examples of bio-based plastics include bio-PE, bio-PET, cellulose acetate, PLA, etc.
What are biodegradable plastics?
Biodegradable plastics can be completely converted to CO2, water and biomass and degraded by microorganisms (e.g. fungi or bacteria) under certain conditions. It does not matter whether biodegradable plastics are produced from fossil or renewable plastics. The process of biodegradation is defined in various standards.
Are all bioplastics biodegradable?
Simply put, no. Because bioplastics are a large family of different plastics that can be either bio-based, biodegradable, or both. However, bio-based does not mean biodegradable. The property of biodegradability does not depend on the raw material base of a material, but is rather related to its chemical structure. Only if microorganisms and fungi, or their enzymes, can cleave and completely metabolize the molecules that make up the plastic is it biodegradable. In other words, biodegradability is a material property.
What are compostable plastics?
For compostable plastics and products, biodegradation must take place within a specified time frame under defined conditions. These requirements are described in the European standards DIN EN 14995 and DIN EN 13432. Depending on the environmental conditions, a distinction is made between composting in industrial composting facilities or garden compost. Certified compostable products can be recognized by certain seals, such as the seedling, DIN industrial compostable, OK Compost INDUSTRIAL, DIN garden compostable and OK Compost Home.
What do the standards DIN EN 13432 and DIN EN 14995 cover?
Biodegradable plastics are considered compostable if they degrade completely within a specified period of time. DIN EN 14995 defines the compostability of plastics in general. DIN EN 13432 specifies the compostability of packaging. The requirements set are the same for both standards and are composed as follows: – Analysis of biodegradation – at least 90% of the polymer mass must have been converted into carbon dioxide within 180 days (approx. 6 months); – Analysis of disintegration during biological treatment. After three months (12 weeks) in industrial or semi-industrial composting conditions, there should be a sufficient level of disintegration, i.e. mechanical disintegration of the plastic (no more than 10% dry mass should remain on a screen < 2 mm). Any residues will also be completely converted to CO2, water and biomass by microorganisms in the further course of time. – Ecotoxicity analysis to show that the biological treatment has not reduced the quality of the compost. This is verified by a plant growth test on compost with biodegraded and disintegrated polymer compared to growth on “normal” compost. – Content of heavy metals and other elements below the limits listed in Annex A.
Are biodegradable materials fully degraded in industrial composting facilities?
Compostable plastics tested and certified according to the European Standard for Industrial Composting EN 13432 must decompose after 12 weeks and completely biodegrade after six months. This means that at least 90 percent of the plastic has been converted into CO2. The remaining portion is made up of water and biomass, which no longer contains any plastic. EN 13432 also includes extensive ecotoxicity tests and testing of heavy metal content to ensure that no harmful substances remain. The resulting compost is of high quality and can therefore be reused as humus. Furthermore, the material thickness plays an important role in meeting the requirements of EN 13432. Thus, the 12-week test period is linked to a maximum material thickness, which is specified in the final results of the respective material tests. However, the vast majority of compostable products, especially compostable bags and pouches, are much thinner and therefore require less than 12 weeks to degrade.
What are drop-in bioplastics?
Drop-in bioplastics are bioplastics whose chemical structure is identical to that of conventional plastics. Bio-PE (polyethylene) and bio-PET (polyethylene terephthalate) are examples of these. The basic building blocks of these bioplastics are made from renewable raw materials instead of petroleum.
Can bioplastics be recycled?
Yes, the resource-saving mechanical recycling established for fossil plastics can also be used without restriction for the bio-based drop-in bioplastics (such as Bio-PE or Bio-PET). These structurally identical bio-based plastics (e.g. Bio-PE, Bio-PET) undergo the same recycling processes as their fossil counterparts and are also materially recycled at high rates. Bio-based compostable plastics, such as PLA, could also be identified using NIR (near-infrared spectroscopy), then sorted out and recycled. However, due to the currently still small quantities of these biodegradable materials in post-consumer plastic mixtures, sorting them out is not yet economical, which is why there is currently no separate material stream. The so-called in-house recycling of production waste is also firmly established for all types of bioplastics in the plastics processing industry. In plastics processing, for example, production waste from injection molding or thermoforming and edge trimmings from film extrusion are already being fed back into the production process as recyclate.
What are the advantages of bioplastics?
Climate change, price increases for fossil materials, and increasing dependence on diminishing fossil resources are all contributing to society’s focus on bioplastics. Bioplastics are innovative, efficient materials that are able to achieve a balance between environmental benefits and the environmental impact of plastics. The biggest advantage is certainly that many bioplastics are made from renewable/renewable raw materials. In this way, they preserve limited fossil resources and, by binding CO2, can help reduce harmful greenhouse gas emissions. Depending on the product, some of our bioplastics guarantee a long service life, while others are biodegradable/compostable and break down into naturally occurring, non-toxic feedstocks. These biodegradable/compostable plastics offer an alternative disposal route. This is advantageous whenever plastics are designed to remain in nature (e.g. tree guards, mulch film, plant clips, plant pots, etc.). Some bioplastics also offer properties that fossil plastics do not. For example, natural breathability, which can extend the shelf life of packaged fresh foods such as fruits and vegetables.
How strong is the demand for bioplastics?
Bioplastics currently account for about one percent of the more than 368 million tons of plastic produced annually. Due to increasing demand as well as the development of innovative biopolymers, applications and products, the market for bioplastics is continuously growing and diversifying. According to the latest market data collected by European Bioplastics in collaboration with the nova Institute, global production capacities for bioplastics will increase from around 2.11 million tons in 2020 to about 2.87 million tons in 2025.
What are the main target markets for bioplastics?
Today, there is a bioplastic alternative for almost every conventional plastic and corresponding application. However, bioplastics offer additional benefits, such as a reduced carbon footprint or additional waste management options, such as composting. As a result, bioplastics are already firmly established in many applications and are being used in an increasing number of industries, from packaging and consumer goods to electronics, automotive and textiles. Packaging remains the largest market segment for bioplastics, accounting for 47 percent of the total bioplastics market in 2020, according to market data from European Bioplastics.
What advantages do bioplastics have for packaging?
Due to their identical properties, bio-based drop-in plastics such as bio-PE or bio-PET are used wherever their fossil counterparts are established but are to be replaced by a more sustainable alternative. For example, in packaging for cosmetics, cleaning products but also food packaging. Biodegradable plastics offer an alternative disposal route, a feature that is particularly important in food packaging for perishable goods. Flexible packaging solutions, such as films and trays, are particularly suitable for fresh products such as fruits and vegetables due to their natural breathability, as they allow for a longer shelf life.
Which bioplastics have the greatest future potential?
Bioplastics, whether biodegradable or structurally identical drop-in solutions, have their place in the material mix. When selecting the suitable bioplastic, the polymer properties, the processing, the recycling as well as the intended or available disposal routes have to be considered. Contact us; together we will find the right bioplastic for your product!
What is PLA?
The abbreviation PLA stands for polylactide, colloquially also known as polylactic acid. This thermoplastic is produced from renewable raw materials and is biodegradable. Nowadays, corn or sugar cane usually serve as the raw material source. PLA is a transparent, brittle plastic with low barrier and heat resistance. By compounding PLA, we can improve the properties and tailor it for the specific application.
Can I make bioplastics myself?
Not only bio-based, but completely biodegradable: Recipe for your own bioplastic! 1 tbsp starch,1 tsp vinegar, 4 tbsp water,1 tsp glycerin (from the pharmacy or drugstore from vegetable fats). Mix all the basic ingredients thoroughly with a whisk and heat in a saucepan over medium heat. Keep stirring until the mixture thickens considerably. Pour mixture into molds or roll out on a baking sheet and let dry. Done! (Source: Science Luxembourg)
Certified soil-biodegradable products / applications
Do certified soil-biodegradable plastics create persistent microplastics?
Biodegradable applications that are certified for soil-biodegradability (e.g. in line with EN 17033 or ISO 23517) are fully biodegradable, i.e. they are converted into CO2, H2O, and biomass. This is guaranteed through the mandatory laboratory biodegradation tests required by the certification (90% mineralization absolute or relative to a positive control within 2 years’ time in soil at ambient temperature, preferably 25 °C). ©europeanbioplastics
Find out moreDo certified soil-biodegradable products fully biodegrade in soil?
Certified soil-biodegradable applications do fully biodegrade in soil. This can be proven by testing and referring to the standard EN 170339 (or ISO 23517 10), which specifies the requirements and test methods for biodegradable applications. ©europeanbioplastics
Find out moreWhat are the advantages of certified soil-biodegradable applications?
Applications made from cerified soil-biodegradable plastics provide significant benefits where retrieval and recycling of conventional plastics pose serious problems. They are specifically designed to biodegrade effectively in situ and can therefore be incorporated into the soil post-harvest. ©europeanbioplastics
Find out moreRelated links
What are Bioplastics?Circular Economy
What is circular economy?
The principle of the circular economy is simple: materials and products should be used, shared, repaired, reused and recycled for as long as possible. Waste should be avoided and natural systems restored. In this way, the life cycle of products is extended. Circular economy has a positive impact on our environment, conserves natural resources and helps create a sustainable competitive, innovative economy.
Find out moreWhat are the benefits of the circular economy for companies?
More and more companies want to produce according to the principles of sustainability: reduce, reuse, recycle. In addition to the positive effects on the environment, the circular economy also offers companies the opportunity to secure competitive advantages, drive innovation and develop new sources of revenue. In this way, they increase their competitiveness, especially in the face of external influences.
Related links
Circular Economy – FKuR knows the right turn!Composting
What are compostable plastics?
For compostable plastics and products, biodegradation must take place within a specified time frame under defined conditions. These requirements are described in the European standards DIN EN 14995 and DIN EN 13432. Depending on the environmental conditions, a distinction is made between composting in industrial composting facilities or garden compost. Certified compostable products can be recognized by certain seals, such as the seedling, DIN industrial compostable, OK Compost INDUSTRIAL, DIN garden compostable and OK Compost Home.
What do the standards DIN EN 13432 and DIN EN 14995 cover?
Biodegradable plastics are considered compostable if they degrade completely within a specified period of time. DIN EN 14995 defines the compostability of plastics in general. DIN EN 13432 specifies the compostability of packaging. The requirements set are the same for both standards and are composed as follows: – Analysis of biodegradation – at least 90% of the polymer mass must have been converted into carbon dioxide within 180 days (approx. 6 months); – Analysis of disintegration during biological treatment. After three months (12 weeks) in industrial or semi-industrial composting conditions, there should be a sufficient level of disintegration, i.e. mechanical disintegration of the plastic (no more than 10% dry mass should remain on a screen < 2 mm). Any residues will also be completely converted to CO2, water and biomass by microorganisms in the further course of time. – Ecotoxicity analysis to show that the biological treatment has not reduced the quality of the compost. This is verified by a plant growth test on compost with biodegraded and disintegrated polymer compared to growth on “normal” compost. – Content of heavy metals and other elements below the limits listed in Annex A.
Are biodegradable materials fully degraded in industrial composting facilities?
Compostable plastics tested and certified according to the European Standard for Industrial Composting EN 13432 must decompose after 12 weeks and completely biodegrade after six months. This means that at least 90 percent of the plastic has been converted into CO2. The remaining portion is made up of water and biomass, which no longer contains any plastic. EN 13432 also includes extensive ecotoxicity tests and testing of heavy metal content to ensure that no harmful substances remain. The resulting compost is of high quality and can therefore be reused as humus. Furthermore, the material thickness plays an important role in meeting the requirements of EN 13432. Thus, the 12-week test period is linked to a maximum material thickness, which is specified in the final results of the respective material tests. However, the vast majority of compostable products, especially compostable bags and pouches, are much thinner and therefore require less than 12 weeks to degrade.
May compostable packaging be disposed of in organic waste?
This depends on the legal regulations that apply in each case. In Germany, according to the Biowaste Ordinance (BioAbfV), only certified compostable biowaste bags are permitted for disposal in the organic waste garbage container. These bags must be made of bioplastics that are certified compostable in accordance with EN 13432 and are based on predominantly renewable raw materials. Approved bags can be recognized by the seedling logo. However, cities and counties have the option of prohibiting their use in their waste statutes. You should therefore find out about local regulations before using them.
How does the industrial composting of bioplastics work?
Industrial composting is a controlled process that can be divided into two phases: active composting (rotting) and subsequent curing (post-rotting). The duration of the active composting phase depends on the type of composting. Currently, compostability criteria for packaging and plastics are very well regulated at European and global level. Compostable plastics that are tested and certified according to the European standards for industrial composting EN 14995 (for plastics in general) or EN 13432 (for packaging) meet the technical criteria for treatment in industrial composting systems. These systems provide controlled conditions, i.e. controlled temperatures, humidity, aeration, etc. for a fast and safe composting process. EN 13432 requires compostable plastics to decompose after 12 weeks and to be fully biodegraded after six months. This means that at least 90 percent of the material has been converted into CO2, water and biomass. Materials and products that meet this standard can be certified and labeled accordingly. The seedling, DIN tested or OK Compost label are well-known marks for products that comply with EN 13432.
Industrial composting vs. garden composting: what’s the difference?
In industrial composting, machines continuously control and adjust the process, temperature and oxygen content. The temperatures in an industrial plant are around 60 degrees. The conditions are optimal so that microorganisms can decompose the organic materials as quickly as possible. However, uniform conditions do not prevail in garden compost. Thus, the processing of organic materials in garden compost takes much longer, especially in cold or very dry weather. You can tell whether a product is industrial or home compostable by the corresponding label.
"I’m green™ bio-based“ products by Braskem
Is the use of pesticides and fungicides a regular practise in plantations?
The main diseases that threaten plants are treated through biological control methods and genetic improvement programmes. As a result, the use of pesticides on sugar cane plantations in Brazil is low, and the use of fungicides is almost zero. © Braskem 2023
What is Braskems responsible ethanol purchasing programm?
Since 2010, in line with the renewable products of the I’m green™ bio-based brand, Braskem developed the Responsible Ethanol Purchasing Programme (RESP), with the aim of ensuring the sustainability of its chain. In 2022, the Programme underwent a comprehensive review with the aim of bringing greater strength to the issues of climate change, biodiversity and human rights. The reformulation of the Programme was carried out in partnership with the Imaflora consultancy and is aligned with the Credibility Principles of the International Social and Environmental Accreditation and Labelling Alliance (ISEAL Alliance).
The Programme’s basic principle is the continuous improvement of the production chain and respect for Brazilian regulations, and is inspired by the good practices described in protocols, certifications and benchmark programmes for the sector, such as Bonsucro. The RESP covers topics such as: business integrity, environment, workers and communities, and the management of sugar cane suppliers. © Braskem 2023
What is the production capacity of I`m Green™ biobased polyethylene plant? Where is the plant located?
The Renewable Ethylene plant is located at the Triunfo Petrochemical Complex, in the state of Rio Grande do Sul, in the southern region of Brazil. It was inaugurated in September 2010, and it was the first time that I’m green™ bio-based polyethylene was manufactured on an industrial scale. The plant’s capacity is 260,000 tonnes/year, and its total investment is US$290 million. © Braskem 2023
What is I`m Green™ bio based logo?
I’m green™ bio-based is the brand created by Braskem that identifies the products in its portfolio made from renewable sources. To identify products that have I’m green™ bio-based polyethylene in their composition and to help consumers recognise them, Braskem created the I’m green™ bio-based label. © Braskem 2023
What is Braskem`s I`m Green™ biobased renewable polyethylene?
Conventional polyethylene is produced from fossil raw materials, such as oil or natural gas, and is found in many day-to-day products: food packaging, cosmetics, drinks, carrier bags, among others. Renewable plastic, also known as I’m green™ bio-based renewable polythene, is a plastic produced from a renewable raw material –ethanol from Brazilian sugar cane. I’m green™ bio-based polyethylene has the same characteristics as petrochemical polyethylene in terms of application, performance and, most importantly, recycling.
© Braskem 2023
What is sugar cane bagasse?
Bagasse is a co-product of the sugar and ethanol production process. Rich in cellulose, bagasse is used to fuel boilers and generate energy in place of gas or other non-renewable energy sources. That energy feeds the plant itself, which becomes energy self-sufficient, and when there is any excess, the energy is sent to the local electricity grid and sold to supply towns and cities. © Braskem 2023
Does the growing consumption of sugar cane ethanol for the production of I`m Green™ bio-based polyethylene have any impact on food production?
Currently, Brazil has 330 million* hectares of arable land, of which 52% is used for livestock, 26% is idle land, and 22% is used for agriculture. Only 1.4%* of all arable land in Brazil is used for ethanol production, and ethanol consumption for the production of I’m green™ bio-based polyethylene represents around 1.7% of total ethanol production, or 0.02% of Brazil’s arable land. The availability of land, combined with the possible intensification of livestock farming, makes Brazil a country with room for agricultural expansion. Even in a very optimistic scenario of growth in the production of chemicals from renewable sources, land use for the production of non-food products is likely to continue to represent a small percentage of the total land available. With specific regard to land management for sugar cane production, in the state of São Paulo, where 50%* of the country’s sugar cane is grown, legumes are used to fix nitrogen in the soil during crop rotation. As a result, 15 to 20% of sugar cane producing areas are used to grow soya, beans and peanuts, supplying the food market. For more details, visit the website of the Sugar Cane Industry Association (UNICA)
Plastics in General
What are plastics?
Plastics are materials consisting mainly of polymers. Polymers are chemical compounds that are synthetically or semi-synthetically produced from monomeric organic molecules. . A distinction is made between three major groups: Thermoplastics, Thermosets and Elastomers. Classic plastics are made from fossil raw materials. They are particularly light, robust, durable, resistant an can be shaped as needed. They also have heat-insulating and electro-insulating properties. Because of these versatile properties, plastics are used in many areas and have become an indispensable part of our everyday lives. Due to the almost unlimited application possibilities and adaptable requirements, plastics offer scope for innovations in almost all areas. Main areas of application are: Packaging, construction and automotive industries, electrical and electronic goods, agriculture, medicine, sports and household goods. Most of the demand for plastics is based on polyethylene of different densities (HDPE, LDPE, LLDPE), polypropylene (PP), polyethylene terephthalate (PET), polyvinyl chloride (PVC) and polyurethanes (PUR).
What does GMO-free mean?
The abbreviation GMO stands for Genetically Modified Organism. If a product is declared GMO-free, it is free of genetically modified organisms
What are elastomers?
Elastomers are dimensionally stable but flexibly formable plastics. The forming takes place under tensile or compressive load. As soon as this load disappears, elastomers return to their original shape.
What are duromers?
Duromers, also known as thermosets, are plastics that cannot be shaped once they have cured. Thermosets are hard, glass-like polymer materials.
What are thermoplastics?
Thermoplastics are all plastics that can be shaped within a certain temperature range. Thermoplastics can be repeatedly melted and cooled.
What is a compoud?
The word compound stands for “mixture”, “connection” or “blend”. Compounds are plastics to which additives, fillers or reinforcing materials are added. In this way, the properties of the plastic can be individually adapted to the requirements of the product to be manufactured or the processability of the plastic can be improved. If two different plastics are compounded with each other, they are also referred to as blends. The production of a compound is called compounding.
What is PET?
PET is the abbreviation for polyethylene terephthalate, a thermoplastic from the polyester family. PET is produced from the monomers terephthalic acid and ethylene glycol. This material is one of the most widely used plastics and is used primarily in textile fibers and the food industry (PET bottle).
Recycling
Can bioplastics be recycled?
Yes, the resource-saving mechanical recycling established for fossil plastics can also be used without restriction for the bio-based drop-in bioplastics (such as Bio-PE or Bio-PET). These structurally identical bio-based plastics (e.g. Bio-PE, Bio-PET) undergo the same recycling processes as their fossil counterparts and are also materially recycled at high rates. Bio-based compostable plastics, such as PLA, could also be identified using NIR (near-infrared spectroscopy), then sorted out and recycled. However, due to the currently still small quantities of these biodegradable materials in post-consumer plastic mixtures, sorting them out is not yet economical, which is why there is currently no separate material stream. The so-called in-house recycling of production waste is also firmly established for all types of bioplastics in the plastics processing industry. In plastics processing, for example, production waste from injection molding or thermoforming and edge trimmings from film extrusion are already being fed back into the production process as recyclate.
What does recyclable mean?
The term “recycle” can be derived from the Latin “re-” for again or back and the Greek word “kyklos” for circle or cycle. If a product is described as 100% recyclable, it can be disposed of and recovered after use via established recycling systems. In this way, waste becomes a new source of raw materials
What does it mean when a product consists of a certain percentage of recyclate?
If a product is advertised as being made wholly or partly from recycled material, it is not virgin plastic that serves as the starting material for manufacturing the product, but rather a reused, recycled plastic. The recyclate comes from post-consumer recyclate (PCR) or post-industrial recyclate (PIR), depending on the requirements of the manufactured product.
What is the difference between a recycled plastic and a bio-based plastic?
A recycled plastic already has already had a “first life” in the form of a product. Through mechanical recycling, separately collected plastics can be reprocessed and used to manufacture new products (“second life”). A bio-based plastic, on the other hand, is made from renewable raw materials. The use of both types of plastic makes absolute sense in order to conserve resources. Products made from bio-based plastic and thus a renewable resource can also be recycled in the end. Unfortunately, infinite recycling is not possible, as the quality of the plastic decreases after each recycling.
What is organic recycling?
Organic recycling allows the biodegradability of plastics to be implemented in a circular way. Organic recycling is an alternative disposal route and is suitable, for example, whenever plastic items are contaminated with food and mechanical recycling would be inefficient. Certified compostable organic waste bags can also find their way into organic recycling. Because they are easy and hygienic to use, they ensure that less organic waste is disposed of in the residual waste garbage can. As a result, the amount of separately collected organic waste can be increased. This serves as fertilizer for plants at the beginning of the cycle.
Can recycled plastics be recycled again?
Unfortunately, infinite recycling is not possible, because the quality of the plastic decreases after each recycling. Therefore, the question cannot be answered in a general way. Rather, after each repeated recycling a decision must be made as to how high the expected further loss of quality is.
What is mechanical recycling?
The recycling of plastics is often carried out by means of mechanical processes, also called mechanical recycling. In mechanical recycling, plastic waste is sorted according to its plastic type, washed, melted down and then processed into recyclates. Recyclates can replace plastics made from virgin material and thus serve as material for new products. The chemical structure of the plastics is preserved during mechanical recycling. Mechanical recycling is an efficient, economical and most climate-friendly process for recycling plastics. Drop-in bioplastics can be collected along with their petroleum-based plastic counterparts through these established recycling systems. The recyclates return to the materials cycle as often as possible until they are used for energy recovery. In this way, energy can be generated from bio-based plastics that do not produce any additional harmful CO2. It is a closed CO2 cycle modeled on nature.
Single-Use Plastics Directive (SUPD)
What is the „Single Use Plastics Directive“ (SUPD)?
The Directive (EU 2019/904) on reducing the environmental impact of certain plastic products, better known as the Single-Use Plastics Directive (SUPD), was adopted by the EU in June 2019 and came into force on July 3, 2021. The directive aims to reduce the amount of plastic waste in the environment, particularly in the ocean. It contains several provisions to achieve this goal.
Which disposable plastic products are banned?
Since July 3, 2021, the EU’s Single-Use Plastics Directive has banned certain single-use plastic products for which there are other material alternatives. This ban affects both single-use products made from conventional plastics and bioplastics. The banned single-use products include cotton swabs, plastic cutlery and plates, drinking straws, stirrers, balloon holders, drinking cups and polystyrene (Styrofoam) food containers for immediate consumption. The EU directive is implemented into national law by the individual member states. In Germany, this has been done through the Single-Use Plastic Ban Ordinance. You can find more information here: https://www.bmu.de/gesetz/verordnung-ueber-das-verbot-des-inverkehrbringens-von-bestimmten-einwegkunststoffprodukten-und-von-produkten-aus-oxo-abbaubarem-kunststoff) and on the Single-Use Plastic Labeling Ordinance (https://www.bmu.de/gesetz/verordnung-ueber-die-beschaffenheit-und-kennzeichnung-von-bestimmten-einwegkunststoffprodukten/
No results for this search